一、项目背景
隶属于浙江A实业集团的浙江B印染有限公司是一家集科工贸为一体的中美合资集染整加工、产品研发、外贸销售于一体的绍兴市级高新技术企业,是中国印染行业协会和浙江省印染行业协会会员企业.公司拥有进口的定型机、轧光机、罐蒸机、丝光机、染色机和喷水织机、剑杆织机160台及配套纺纱、拼线花式丝设备30余台套,日加工能力25万米以上。
该印染企业集中体现了印染行业的运营特点:致力于纺织印染行业新产品开发,关注设备技改和生产工艺改善,提高产品附加值,并参与纺织品高端市场的竞争。以提高科技含量,提升产品档次,做好流行色的研发及染色技术应用为己任,注重培养和提高员工业务技能,满足市场对印染日新月异的发展需求。
企业虽然走出了低谷,但现场规范化管理亟待提升。“整体不规范”是现场管理的共同特征:有限的空间,被放置凌乱的物料占用;墙角堆放的待修、待退品长期未处理;布车放置未定点定位,毫无章法;墙体破损,墙面脏乱;没有设立通道,物流不畅;作业区,周转区没有明确规划;机台防护未到位,多数存在安全隐患;地面损坏,未修复;员工物料堆放行为很随意;私人物品放置点没有设立;员工饮水不便利;称料间物料放置混乱,称量行为不规范,作业环境较恶劣;白坯/成品库物料堆放未规范,放置点不受控;缺少相关信息显示看板,下达的信息多为临时张贴或口头传达;员工及基层主管缺乏整理整顿观念,规范意识淡薄。现场诸如此类的现象随处可见。
为了使企业内部的生产运营提升到一个新的高度,怡创印染对企业现场5S管理的全面改善需求非常迫切,良好的现场环境不仅可以对外展示企业的形象,而且有助于提高员工的素养,提高生产效率,实现安全生产,减少浪费,为企业进一步发展奠定坚实的基础。
经过深入交流,该印染企业高层决定聘请汇成企业管理咨询公司帮助企业进行5S管理提升活动,并对此项活动寄予高度期望;要求现场5S管理活动做到实处,做到细处;通过这项活动,使企业管理人员树立现代企业管理观念,提高全员素质。
二、调研分析和结论
B企业分设有两个及两个以上的多个车间,咨询组选取其中问题最多、改善难度最大的车间:生产一车间首先进行改善,目的是从中摸索在该企业所有车间推动系统性5S改善的经验,树立示范,一定程度上复制并推广。
咨询组从以下几个方面对试点车间的现场管理现状进行调研分析:
●该车间是否接触过5S管理理念;
●该车间目前在现场管理方面实际上采取了哪些管理措施;
●该车间的现场管理有哪些主要问题;
●在即将实施的现场管理活动中,需注意哪些生产现场特性;
经过和车间领导班子成员进行座谈及现场走访,我们了解到,多数车间主管都是浅层次的了解一些现场管理概念,曾在总公司的要求下,开展过文明生产。但对现场5S管理远没有形成系统性观念,企业对车间员工有一些关于保持环境卫生、着装要求以及劳动纪律等方面的考核,但有些条款缺乏操作性。例如,如果不是当场抓住谁丢的垃圾,就无法将考核落实到人。至于如何改善现场生产作业环境,提高安全生产水平,企业缺少行之有效的系统方法动员和组织员工开展改善活动,车间整体环境也不利于培养员工的素养。
咨询人员和车间主管一同对车间现场进行了调查,并用数码相机对突出问题进行拍照。调查目的不是确定哪里要改善和如何改善,而是为下一步进行系统性5S管理活动动员会收集资料。5S管理咨询的实际操作性很强,看似简单直接,实际上涉及生产、技术、安全、设备维护、成本核算等诸多环节。在咨询过程中,咨询人员应发挥自身的优势,更多地起到培训、提供方法、动员、组织活动、评价的作用,具体的改善方案在企业内部人员提出的基础上优化完善并组织落实。只有咨询人员与企业管理人员密切配合,5S系统性管理咨询才能取得良好的预期效果。
经过调研分析,咨询人员认为,试点车间虽然在现场管理中存在很多问题,但相关主管有一定的抓文明生产的经验,愿意接受5S管理的思路,在管理制度上具备一定的基础,这些是有利条件。下一步,咨询人员将根据自身的工作定位,对各级管理人员进行理念培训、推动建立车间5S管理的组织体系、细化项目实施明细、组织开展活动,同时构建5S管理长效机制,与企业及车间管理人员共同推动5S管理的提升,并初步确立了“硬件先行”的指导思想和“行为决定思维”的推进策略,据此开展印染企业现场5S管理的“诊治疗法”。
三、策划思路及方案实施内容
1.召开5S管理动员会
企业高层领导、职能部门及车间主管参加动员会。咨询人员根据调研分析时收集的素材,结合试点车间的发展要求,讲解了5S管理的基本概念和重要性。随后,分厂总经理作动员发言,要求各单位领导高度重视此次系统性现场改善咨询,密切配合咨询组做好5S管理提升。
2.展示各区域在系统化整改后的初步效果图,建立愿景
整体改善方案PPT演示讲解。内容包括:
●需整改及完善的对应区域;
●对应区域需整改及完善具体内容;
●每个区域整理整顿粗略完成时间;
●5S活动中需配合的注意事项;
●展示完成后的现场局部效果预设图;
3.推动建立5S管理组织
成立由总经理担任组长的5S项目小组,由生产部、工艺组、设备科、机电组、质检部、仓管部等相应负责人担任小组组员,负责推动企业5S管理活动开展,对各作业管辖区域开展活动的效果进行检查评价,并负责在公司5S小组和咨询人员的领导下,组织下属员工的5S管理提升。
4.系统性整改方案设计
以全面改善的思想和硬件现行的思路,结合前期现场调研,提出具体并可实际操作的全面整改明细:
⑴现场全面整理
以要和不要为判别基准,用不超过一周的时间对现场全面整理,对现场多余的物料、角落的垃圾、地面的积水、损坏的布车、张贴的宣传品、长期不用的柜子、废弃的老旧设备等作全面清理,为现场腾出空间,也为后期相关实施项目提供便利条件。
⑵车间整体平面布局图绘制
咨询组先期按比例测绘车间平面图及设备布局图,为后期各项目实施提供图上作业参考,并从图上显示其机台/通道/物流等布局不合理性,作图纸合理性修改,减少现场开展活动时的出错概率。
⑶安装墙角角铁及墙体/机台防护栏
对车间所有墙角安装包边角铁,墙体及机台安装防护栏杆,并统一标准油漆。
⑷修复墙面/涂料油漆
先行修复各处破损老旧墙面,并刷白。按规定尺寸进行墙面墙裙涂料粉刷。
⑸设置车间通道/消防通道
按物流流向属性,设置布车及人行过道;按消防规定要求,规划并设置消防通道,设置硬件,做到消防区域不堵塞,不占用。
⑹设置布车区,规划灯箱区位布局
按生产流程属性,设置再用布车区,周转布车区,空车区。对应布车区设计区位显示灯箱,实施钢丝悬挂和空中走线。
⑺设置区域标识标牌
车间原有各生产单元无明显标牌识别,尤其仓库库位标牌更显为重要。针对这点,咨询组会同各职能部门,汇总生产单元标准识别名称,汇总仓库库区纵横坐标标牌,汇总办公部门对应标牌名称。汇总后经标准设计,经高层审核后,由广告公司专业制作并现场安装。
⑻称料间系统性改造
称料作为染缸工序的前期准备动作,重要性尤为突出,现有的称料间(粉剂/助剂/化料),无论在现场称量环境及物料放置规范,还是在称量方法上,整体状况堪忧。咨询组树立一个全新的观念:系统性改造称料间。并将实施内容分解:
●地面及墙面磁砖铺设
●磁砖台面建造
●地面排水槽建造
●区域内定点定位规划
●染化料放置容器按标准统一购买
●各类搁台/搁架设计制作并安装
●照明改造
●通风设施改造
●染料称量系统灯架/工控显示灯制作安装
●称量电脑系统上线
●对称料人员培训上岗
⑼白坯/成品库区划
白坯/成品库分别作为前期入库和后期出库的转道场地,在定点定位上,需要堆放明确,显示清晰,盘库便捷。按这三点基本要求,咨询组绘制库区平面图,和仓储主管共同构建仓储思路:建立仓储现场棋盘模型;实施地面线框和栏杆施工;实施纵横坐标标牌显示;实施每个堆放单元地面编号;设立搬运工具放置区;设立现场电脑操作站点;颁布仓储基本操作规则。
⑽设置私人物品放置用具/清洁工具
根据车间现有的员工物品放置柜和清洁用具,主要是优化放置区域,完善放置要求,实施定点定位,淘汰和更新部分硬件,制定放置规则和考核制度。
⑾设置饮水区
针对现场饮水区单一的现状,咨询组提出建造饮水区的方案,并得到一致认可,根据平面图,由咨询组拿出方案明细;平均分布设置点;施工队实施饮水区地面磁砖铺设;机修科实施饮水区栏杆安装和水杯架制作;采购部落实饮水机/连体桌椅/垃圾桶购买;电工组落实水管和电线到位。
⑿监控点布局调整及完善
根据安全生产及现场巡检的要求,对原有的监控点做全面检修和布局调整,完善现场监控盲点,做到各作业单元均在监控可视范围。
⒀信息看板制作
员工对车间的整体信息了解渠道很少,仅靠偶尔张贴的通知通告获取,针对此点,咨询组根据现场监控的视频和巡检日常工作提供的素材,建立屏风看板和电视信息显示,将安全警示、违规操作、未规范行为、考核统计等信息集中动态显示,使员工在了解车间整体运行情况时,规范自身的各项操作行为。
⒁辅助规划冷堆控制
原有的冷堆处理方法很粗放,无法达到实效控制和自动时点提醒,咨询组提出实施工控警报装置,结合现场布局,落实冷堆放置场地,规划工控实施系统,由咨询组/机修部/电工组联合落实,这是现场管理细节的一大提升,也是车间一道亮丽的风景。
⒂制定5S管理制度工作
●根据生产单元划分5S责任区;
●设置现场巡检岗位,配置巡检工具,培训上岗;
●建立并实施5S检查和责任奖罚制度;
●由巡检员落实月度现场管理工作汇报。
5.各项目清单实施明细计划表
针对现场全面改善的系统性和事项开展的繁杂性,为确保整体方案的有序实施和细化责任落实的要求,咨询组制定各月度详尽的项目推进计划表(甘特图),格式如下:
X X月份项目推进计划
项目
|
作业内容
|
序
|
任务分解
|
X X月份时间
|
责任人
|
企业作业
|
|
|
|
|
|
|
A项实施方案
|
分解内容B
|
1
|
XXX
|
作业项E
|
|
|
|
|
|
|
分解内容C
|
2
|
XXX
|
作业项F
|
|
|
|
|
|
|
分解内容D
|
3
|
XXX
|
作业项G
|
|
|
|
|
|
|
- - - - -
- - - - -
|
- - - - -
|
-
|
- - -
|
- - - -
|
|
|
|
|
|
|
- - - - -
|
-
|
- - -
|
- - - -
|
|
|
|
|
|
|
●项目:明确现场全面改善设计框架;
●作业内容:将项目分解为各项可操作行为;
●序:明确作业内容分解数量;
●责任人:明确作业内容由相应部门相应人员落实;
●企业作业:明确并落实企业在各项活动中的相关行为;
●月份时间:明确时间观念,显示各项目分解任务的完成进度。
通过该详尽的推进计划表,落实单项作业内容,落实对应责任人,落实企业作业项,明晰完成时间,使得整体项目在同步推进时可动态协调控制,该计划每个月初由咨询组撰写,由企业审核修改通过,在各月度工作总结时,能详细展示各项进展状态。
6.全面推广
通过对试点车间的系统性现场改善后,咨询组在方案设计上有了丰富的第一手资料和程序上的方法总结,在即将推广现场改善的其他车间,各部门主管也对现场整改有了学习的参照和个人的感悟,并先期提出自己的一些改善观点,咨询组根据即将推广的车间局部特点以及对其相关主管的调研,随后策划了全面整改设计内容和推进计划,落实了5S管理的程序和方法,染整分厂的现场全面整改和完善工作就此全面推广,怡创印染也将在完成一车间整改后全面推广。
7.建立5S管理长效机制
为了使5S管理活动成为企业日常管理的一部分,避免5S管理只成为一时的活动,咨询组为企业建立了5S管理的长效机制,主要有两部分组成:
⑴由后期专设的现场巡检,强化日常巡检工作,通过监控视频,通过现场拍照,通过巡检考核,通过月度工作报告,综合强化现场规范行为,持续提升员工规范观念。
⑵将现场巡检工作岗位纳入企业工程管理部范畴,并接受管理工程部的月度现场检查和考核,对安全隐患、操作行为、设备运转、现场规范、车间环境等作全面检查和整改,在公司整体考核机制下,强化各车间自身5S管理持续提升。
四、遗留问题及进一步改善思路设想综述
●遗留问题:⑴在后期具体推行活动中,高层考虑到成本性的问题及个人观念,部分方案细节被简化或暂停,如称料间改造上,现场方案施工被简化,除称料系统外,只在原有基础上稍作整理整顿,改观欠佳;饮水区设计上,外观形式要求简单化,布局数量也减少;染缸区的地面排水及设计效果方案也未执行。⑵方案执行进度上部分落后于计划,使得后期项目实施部分延缓;局部现场调整是企业自己临时的行为,如已规划好的仓库被扩展的打样室占用较多库区;现场新购机台/车间机台调整,对已规划好的布车区、仓库区及通道区均有较大影响。
●改善思路设想:建立项目执行制度,严肃执行纪律;关注方案最终实效性和表现形式美观性;更多的注重实效图绘制,依此效果说服人;针对企业局部现场的新变化,对方案规划作同步变动,并切合新变化的需要;若干单个项目实施预算,在预算范围内求精。
五、方案实施效果
通过咨询组和企业的共同努力,企业在系统性的5S现场整改后,用半年多的时间,使得现场规范效果大为转变,现场效果也正在凸显之中:
●布车按作业区和周转区定点定位,规范有序;
●布车区位灯箱设立,使得布车在系统查询时变得快捷;
●设立车辆及消防通道,人及物流流转通畅;
●现场全面整理,无多余及废弃物料和设备,视野变的开阔;
●墙体修复,墙裙涂料油漆,视觉效果改善;
●墙面及设备防护栏安装,大幅度降低被碰撞的损坏程度;
●饮水区的全面建立和个性化的设计为员工提供直接便利;
●称料间系统性改造,改变了现场风貌和员工的称料行为及态度;
●白坯/成品库规划,使得物料堆放规范,搬运明确,查询便捷;
●信息看板的设立,强化员工的规范观念,提升整体规范素养;
●冷堆的现场管控,强化了冷堆时效性,也固化了员工行为规范;
●员工的规范操作行为由以前的被动变为主动,减少管理难度;
●现场巡检工作及制度,使得未规范行为有人可管,有法可依。
该项目的5S全面整改案例,打造了一次全面性的现场“诊治”,“诊治了”作业环境,“诊治了”现场规范,“诊治了”操作行为,“诊治了”员工观念。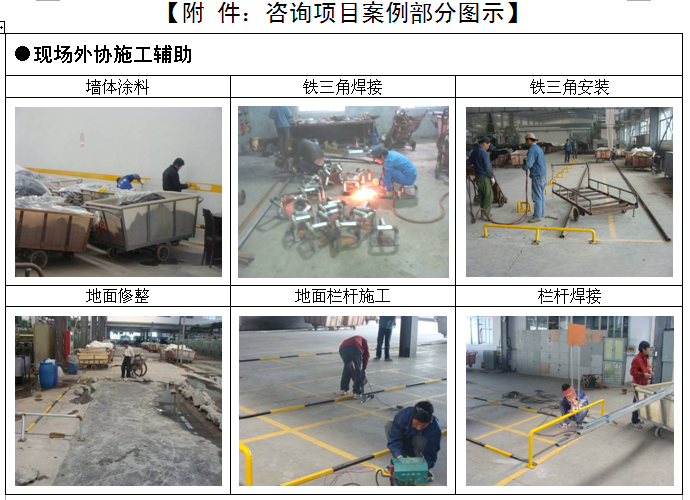
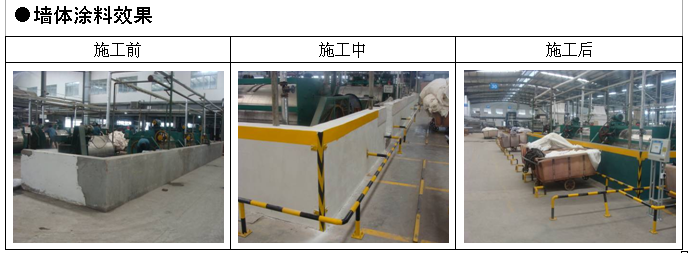

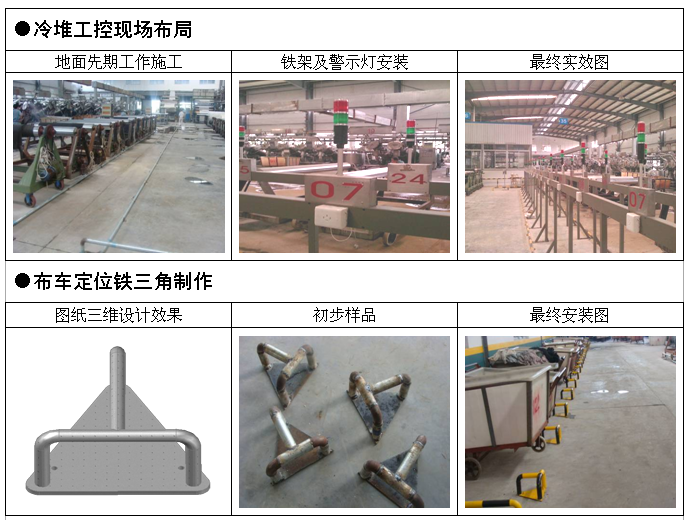
